How are solar panels made, and what methods are used to ensure solar panels can reliably and efficiently harness the sun’s power?
How are solar panels made, and what processes ensure they can reliably and efficiently capture the sun’s energy?
Understanding the manufacturing process of solar panels is essential to appreciating their role in the shift towards sustainable living and an energy-independent future.
Solar panels are a vital component in the global push for cleaner energy, with their adoption continuing to rise. As of July 2024, the UK alone boasts 17.0 GW of solar capacity across 1,612,381 installations.
The production of solar panels begins with the creation of solar cells from pure silicon, a process that requires precision and advanced technology.
These cells are then meticulously assembled and connected to form a solar panel. A protective back sheet is added, and the entire structure is enclosed within a durable frame to ensure longevity and effectiveness.
In this guide, we’ll take you through a step-by-step overview of how solar panels are made, from the initial preparation of raw materials to the final assembly, highlighting the key methods and technologies involved in producing high-quality solar panels.
Pro tip: Avoid upsells and confusing packages—choose a provider with a clear, fixed-price quote that won’t change. Heatable, a Which?-approved solar installer, offers transparent pricing with no surprises.
Step 1: Raw Materials and Silicon Processing
Silicon is the core material used in most solar panels, and it must be highly purified to function effectively. The production process starts with the extraction of silicon from sand or quartz.
The silicon is then processed at very high temperatures in an arc furnace to create pure metallurgical-grade silicon (MGS).
Want to Save Money with Solar Panels?
- MCS-accredited & Which? Trusted Trader
- Exclusive REA Fusion solar panels
- Fixed price guarantee — no hidden fees
- Finance options & deposit protection
- Average 4.9/5 rating from thousands of happy customers
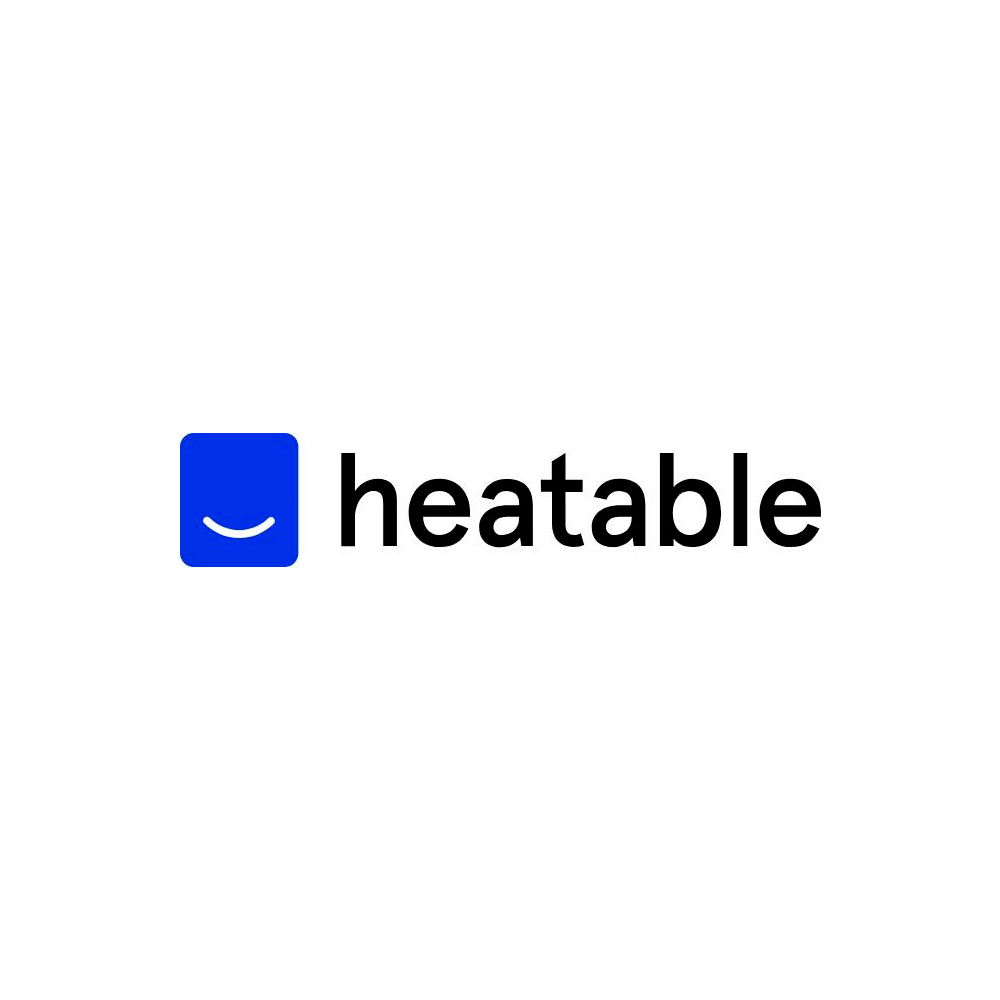
The MGS is further purified to achieve high-purity polysilicon through the Siemens process.
This involves heating the silicon in a reactor with hydrogen chloride to produce trichlorosilane, which is then distilled and decomposed at high temperatures to create pure polysilicon.
Get a free estimate for your solar with the experts at Heatable:
- It’s free, easy, and without obligation
- Compare quotes & get the best prices
- Save up to £660 per year
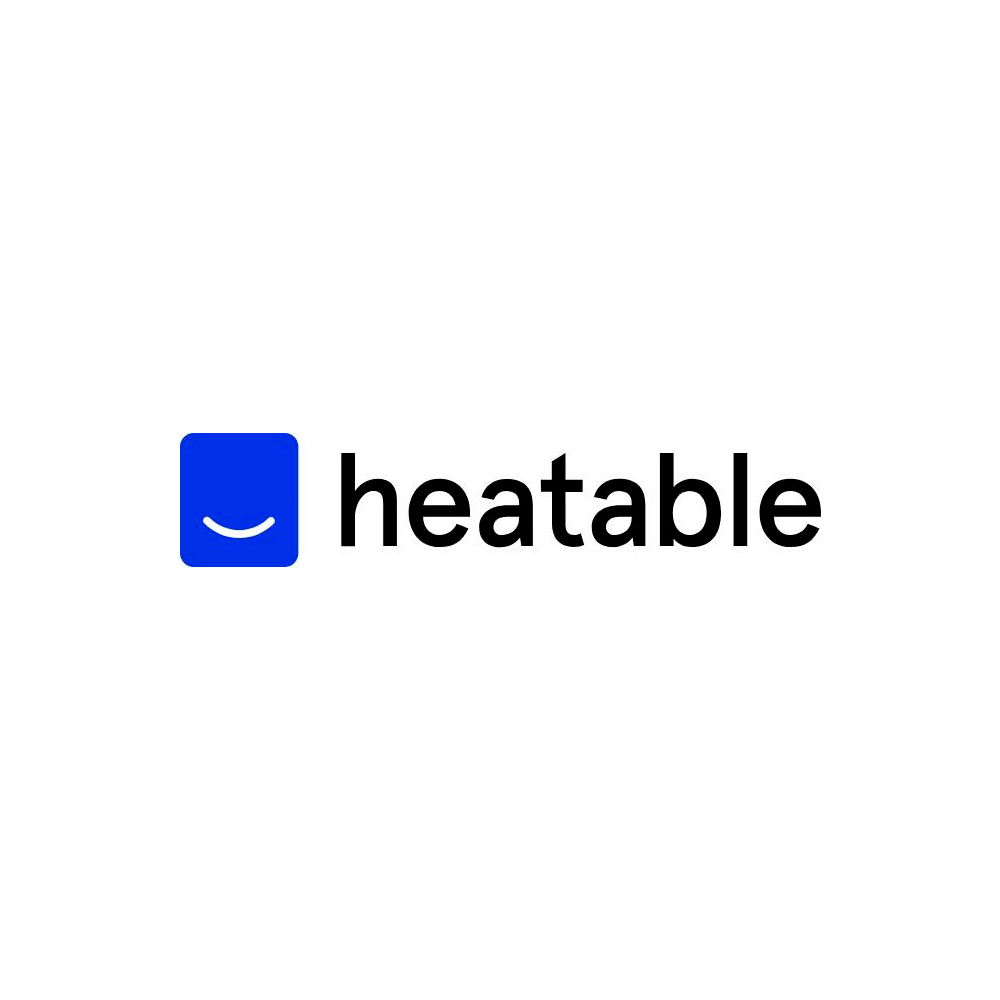
Step 2: Silicon Wafer Production
The next step involves producing silicon wafers. The polysilicon is placed into a container that is heated until it forms a liquid mass.
The liquid mass is slowly cooled until it solidifies from the bottom up, creating a large-grained multicrystalline silicon ingot.
Silicon ingots are then sliced into very thin wafers using diamond-coated wire saws. The wafers form the base of the solar cells, and irregularities are removed before further processing.
Step 3: Solar Cell Fabrication
The next step involves fabricating the silicon wafers into photovoltaic (PV) cells. The wafers are treated with dopants (typically phosphorus and boron) to create a positive (p-type) and a negative (n-type) layer.
This process enhances the electrical conductivity of the silicon and forms the p-n junction critical for the photovoltaic effect.
An anti-reflective coating is then applied to the surface of the silicon wafers to maximise light absorption.
The coating reduces sunlight reflection and increases the cells’ light absorption.
Metal conductors are then screen-printed to the front and back of each wafer to form the grid pattern necessary for electrical connectivity.
Step 4: Solar Panel Assembly
After fabricating the solar cells, they undergo rigorous testing to meet quality standards.
They’re then connected in series or parallel configurations to form a solar panel by soldering tabs to the cells and connecting them with conductive ribbons.
The panels are then assembled through a few stages:
- Lamination – The interconnected cells are sandwiched between protective layers, including an ethylene-vinyl acetate (EVA) layer, which acts as an adhesive. This assembly is placed in a lamination machine that heats and presses the layers together, ensuring the cells are securely encapsulated.
- Framing and Glass Covering – The laminated panel is fitted with a durable aluminium frame, providing structural support, durability and protection. A layer of tempered glass is placed on the front of the panel to shield it from environmental elements while allowing maximum light transmission.
- Backsheet and Junction Box: The back of the panel is covered with a protective back sheet, which prevents moisture ingress and provides insulation. A junction box is attached to the back of the panel, housing the electrical connections and facilitating the integration of the panel with other system components. The junction box collects the electricity the cells produce and controls the electricity sent from the panels to the rest of the system.
Step 5: Quality Control and Testing
Once the solar panels are assembled, they undergo rigorous testing before being sold or installed. The quality control and testing process involves the following:
- Visual Inspections – This ensures the physical integrity of the panels. They’re checked for any visible defects such as scratches, cracks or manufacturing flaws.
- Electrical Testing – The panels undergo various electrical tests to ensure they meet specifications and verify their safety and functionality. It includes measuring the overall efficiency, short-circuit current and open-circuit current.
- Performance Testing — The panels are tested under Standard Test Conditions (STC). This simulates sunlight conditions to ensure they perform as expected and measure their electrical output. The tests help determine whether the panels meet the specified efficiency levels and power ratings.
- Mechanical Testing — The panels are subjected to various mechanical stress tests to assess their durability and resistance to environmental conditions. These can include humidity, high temperature, and mechanical load tests to ensure they can withstand harsh conditions and stresses like strong winds and snow loads.
- Compliance and Documentation — The panels are certified to ensure they meet national and international industry standards, such as those set by the International Electrotechnical Commission (IEC). This involves maintaining comprehensive test result documentation for traceability and compliance and providing customers with detailed reports on installation, performance, and safety checks.
How Can Manufacturers Ensure Sustainability in Solar Panel Production?
Manufacturers should focus on reducing the environmental impact of panel production by recycling materials, minimising waste and using eco-friendly processes.
Silicon extraction involves mining quartzite, which can cause pollution and habitat destruction if not managed correctly.
The production of silicon wafers also requires substantial energy. Using renewable energy instead of fossil fuels in manufacturing can reduce the overall carbon footprint and mitigate any impacts.
Making solar panels can also generate a lot of waste, including slurry and silicon dust. Efficient waste management and recycling practices are also essential to reduce environmental impact.
Recycling is also important for solar panels that have completed their lifespan. It can help reduce landfill waste and recover valuable materials.
Related solar guides:
- How many solar panels do you need?
- Smart Export Guarantee
- Can you install solar panels in a conservation area?
- Best 4kw solar system with battery storage
- Sunshine hours map UK
- Best Solar Panels
- Solar panel output calculator
Final Thoughts on How Solar Panels Are Made
Understanding how solar panels are made can help you make an informed decision when investing in solar technology.
The entire process, from raw material preparation to final assembly, quality control and testing, is dedicated to reducing environmental impact, advancing technology and contributing to a more sustainable future.
Sources and References
- https://www.gov.uk/government/statistics/solar-photovoltaics-deployment